Efficiency is everything. But behind every efficient operation lies a well-maintained system—especially when it comes to your equipment. From small tools to heavy machinery, equipment maintenance often doesn’t get the spotlight it deserves. Yet, it's the very thing that can make or break your productivity, cost control, and safety outcomes.
If you’ve ever had a job delayed because of a faulty leaf blower or an unresponsive liftgate, you know the pain all too well. Establishing clear, standardized maintenance procedures isn't just best practice—it's a necessity. In this guide, we’ll walk you through the why, what, and how of equipment maintenance procedures tailored specifically for fleet managers.
Why Maintenance Procedures Matter More Than You Think
Most fleet managers already follow some form of vehicle maintenance schedule. But equipment maintenance often flies under the radar—until something breaks, downtime kicks in, and costs start piling up.
Here’s what solid equipment management procedures bring to the table:
- Increased uptime: Tools and machines last longer and break down less often.
- Improved safety: Regular maintenance prevents hazardous failures.
- Lower costs: Fewer surprise breakdowns mean fewer expensive repairs.
- Better compliance: Well-documented procedures help meet safety and regulatory standards.
- Data-driven insights: Tracking trends helps make smarter purchase and replacement decisions.
Simply put: what you maintain performs. And what performs saves time and money.
What Are Equipment Maintenance Procedures?
Maintenance procedures are structured instructions that outline how to inspect, service, repair, and maintain your tools and equipment. Whether it’s a power drill, pressure washer, or crane, having a written process keeps things consistent, safe, and efficient.
Each maintenance procedure should clearly define:
- What equipment is covered
- Tasks to be performed
- Tools and materials required
- Safety precautions
- Frequencies and schedules
- Documentation standards
Think of it as your playbook for extending the life of your assets—and avoiding operational chaos.
Download our free Excavator Safety Checklist
Key Components of a Good Maintenance Procedure
Creating standardized procedures doesn’t need to be complicated. Start by covering the essentials:
Description
A brief summary of what the procedure involves and why it matters.
Scope
Define the boundaries—what parts or types of equipment the procedure applies to.
Safety Guidelines
Outline protective gear, lockout/tagout rules, and any relevant hazards.
Tools and Materials
List everything the technician needs: replacement parts, lubricants, PPE, etc.
Step-by-Step Tasks
Clear, actionable instructions. Use bullet points for readability.
Frequency
How often should this task be done? Daily, weekly, or monthly?
Documentation
How and where should the technician record what’s been done? Ensure traceability.
Responsibilities
Who does what? From inspections to sign-offs, assign roles clearly.
Steps to Create Effective Standard Maintenance Procedures
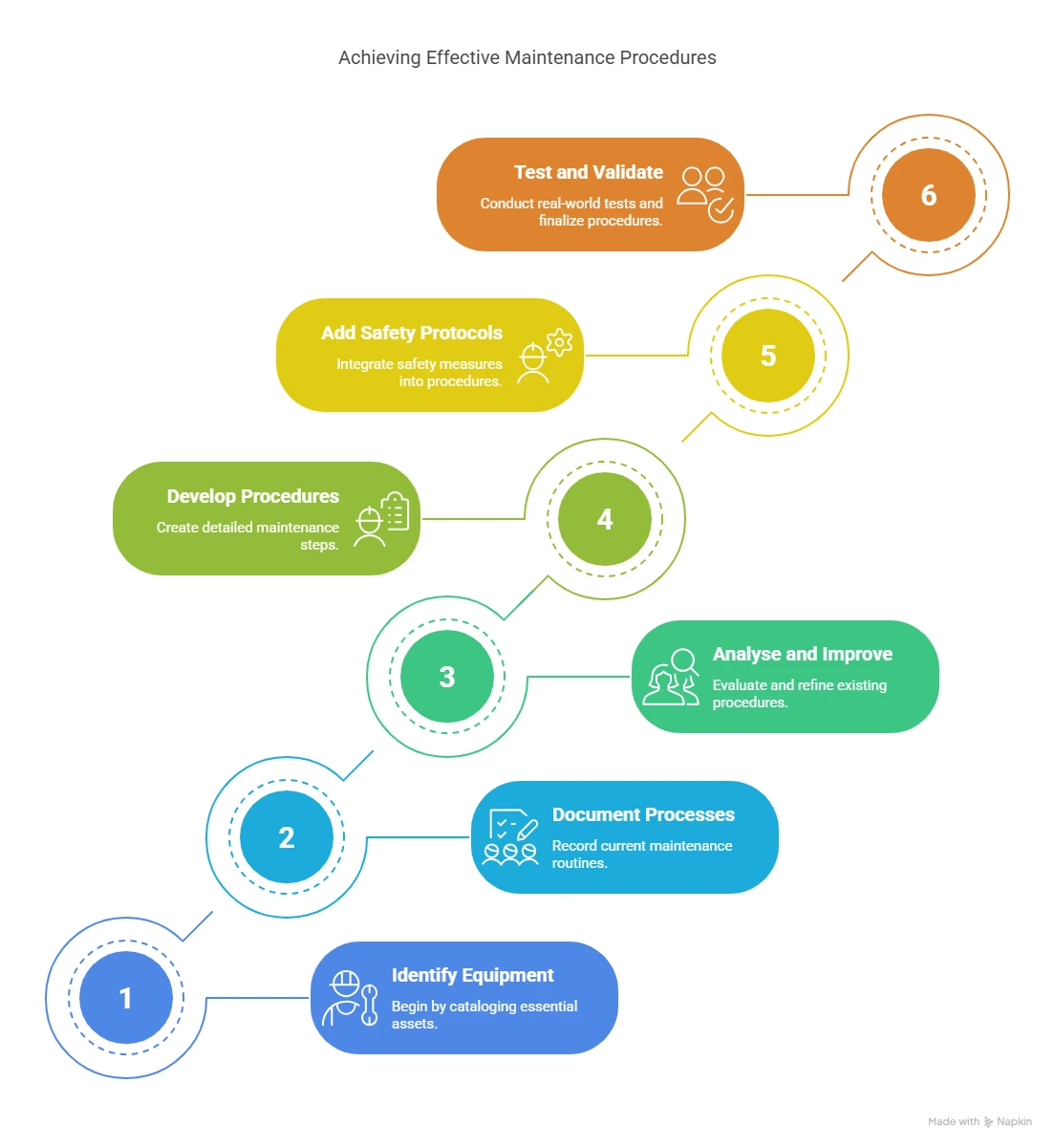
A successful maintenance strategy starts with standardization. Here’s a roadmap to get you going:
Step 1: Identify Your Equipment
Start with an inventory. Focus on high-value, frequently used, or safety-critical assets. Don’t overlook small tools—losing a single wet vacuum on a job site can slow down an entire team.
Step 2: Document Existing Processes
Even if your team has informal routines, write them down. Understand what’s currently done, what works, and what doesn’t.
Step 3: Analyse and Improve
Look for inefficiencies or safety gaps. Get input from the technicians who use the equipment daily.
Step 4: Develop Detailed Procedures
Draft clear and concise steps for each maintenance task. Include photos or diagrams where helpful.
Step 5: Add Safety Protocols
Integrate safety at every step. A safe technician is a productive one.
Step 6: Test, Verify, and Validate
Run the procedure in real conditions. Get feedback. Adjust and finalize based on what works best on the ground.
Use Technology to Make It Easier
Managing everything manually—on whiteboards, spreadsheets, or printed forms—is a recipe for inconsistency and missed maintenance. That’s where a Computerised Maintenance Management System (CMMS) or fleet management software comes in.
Here’s how software makes life easier:
- Automated Scheduling: Set reminders for preventive maintenance based on usage or time.
- Mobile Inspections: Let field crews complete checklists from their phones.
- Work Order Management: Log, assign, and track issues from identification to resolution.
- Data & Reporting: Understand trends, costs, and performance at a glance.
- Safety Compliance: Integrate safety checks directly into digital workflows.
If you’re still tracking service history in Excel or filing repair notes in a drawer, it’s time to upgrade.
Implementing the Procedures: Where Most Fleets Go Wrong
Creating a procedure is only half the job—getting your team to follow it is where things often fall apart. Here’s how to make it stick:
- Training and Education: Ensure every technician knows the procedure, understands its purpose, and can follow it confidently. Consider certifications or refreshers every six months.
- Daily Integration: Embed procedures into your work orders and job flows. Make them part of “how things are done” from day one.
- Feedback and Monitoring: Create a feedback loop. Encourage technicians to share what’s working and what’s not. Adjust procedures based on real-world use.
Final Thoughts: Your Next Steps
In fleet management, equipment is more than just an asset—it’s your frontline tool for getting the job done. Without proper maintenance procedures in place, even the best tools won’t last.
Start small. Standardize one or two procedures. Choose a user-friendly maintenance platform. Involve your team. Train them well. Over time, you’ll build a system that not only protects your equipment but also strengthens your entire operation.
Ready to streamline your fleet’s equipment maintenance? It starts with the right tools and the right strategy.