Key Takeaways
As a construction manager, you already know how critical heavy equipment is to the success of your projects. These machines, from excavators to dump trucks, are the backbone of your operation. But managing their maintenance? That can feel like a never-ending challenge. Whether it’s keeping up with wear and tear, preventing breakdowns, or ensuring that your fleet is always running smoothly, heavy equipment maintenance can become a major headache. The good news is, that with the right strategies in place, you can minimize downtime and maximize the lifespan of your machinery.
Why Heavy Equipment Maintenance Feels Like a Constant Battle
Let’s face it—you’re dealing with tough conditions every day. Construction sites are harsh on machinery, with dirt, debris, moisture, and constant use causing significant wear and tear. Even the most durable equipment can suffer under these conditions, leading to frequent breakdowns, costly repairs, and delays. And when equipment fails, it’s not just an inconvenience. It can halt entire projects, stretch budgets, and eat up your valuable time as you scramble to get things back on track.
But the real challenge? Staying ahead of these problems before they happen. You’re managing a lot—people, projects, deadlines—so it’s easy for equipment maintenance to fall to the bottom of your to-do list. But neglecting it can have serious consequences, from safety risks to higher operating costs.
How Proactive Maintenance Can Save You Time and Money
The key to minimizing headaches and keeping your construction site running smoothly is to take a proactive approach to heavy equipment maintenance. Instead of waiting for something to break, you can prevent problems from happening in the first place. By investing a little time and effort into routine maintenance, you can avoid the bigger, more expensive problems down the line.
Here’s how proactive maintenance can benefit you:
- Minimize Downtime: Preventative maintenance keeps your equipment in top shape, reducing the chances of unexpected breakdowns. Less downtime means your projects stay on schedule.
- Lower Repair Costs: Fixing small issues during routine inspections is much cheaper than dealing with a major breakdown. A regular check-up can catch potential problems early, saving you from costly repairs.
- Extend Equipment Life: Well-maintained machines last longer, which means you’ll get more mileage out of your investments. This extends the time before you need to consider expensive replacements.
- Improve Safety: Malfunctioning equipment isn’t just an inconvenience; it’s a safety risk. Regular maintenance ensures your machinery operates safely, protecting your workers and reducing liability.
Why Preventive Maintenance Matters for Heavy Equipment
- Reduces Downtime: Regular maintenance helps prevent unexpected equipment failures, ensuring machinery stays operational and projects remain on schedule.
- Avoids Costly Repairs: By catching issues early, preventive maintenance reduces the need for expensive emergency repairs and fixes.
- Improves Equipment Longevity: Consistent upkeep extends the life of heavy equipment, delaying the need for costly replacements.
- Cost-Effective: Preventive maintenance is more affordable than reactive maintenance, which can result in expensive repairs and unexpected downtime.
- Heavy Equipment Maintenance Checklist: Regular tasks such as oil changes, tire inspections, and hydraulic system checks should be part of a heavy equipment maintenance checklist to ensure all aspects of the equipment are functioning properly.
- Safety Improvement: Routine inspections and maintenance help identify safety risks, reducing the chances of accidents or injuries on the job site.
- Best Practices for Preventive Maintenance:
- Perform routine inspections at regular intervals.
- Keep detailed maintenance records to track repairs and replacements
- Use software or tools to monitor equipment performance and identify potential issues early.
By adopting these practices, construction managers can reduce unexpected breakdowns, improve equipment performance, and enhance the safety and efficiency of their teams.
Heavy Equipment Maintenance Checklist
A well-organized heavy equipment maintenance checklist ensures that all critical tasks are performed regularly, reducing the risk of breakdowns and enhancing the longevity of machinery. Below is a detailed checklist organized by equipment type:
Best Practices for Maintaining Heavy Equipment
Now that you understand the value of proactive maintenance, let’s dive into some best practices that can help you keep your equipment in great shape.
.avif)
1. Create a Regular Maintenance Schedule
One of the most effective ways to stay on top of equipment maintenance is to set up a clear, consistent schedule. You can’t rely on memory or assume you’ll catch problems as they arise—things get busy, and maintenance can slip through the cracks. Having a dedicated schedule helps ensure your equipment is being inspected and serviced regularly.
How to do this:
- Work with your equipment manufacturers to follow their recommended maintenance intervals.
- Customize your schedule based on how frequently you use each piece of machinery.
- Set reminders for routine inspections, oil changes, filter replacements, and other critical tasks.
By having a detailed plan, you’ll prevent maintenance tasks from piling up, and you’ll address issues before they become serious problems.
2. Conduct Pre-Operation Inspections
Before you put any piece of equipment to work, it’s essential to conduct a quick inspection. This can catch obvious issues before they cause trouble. A simple checklist can guide you or your team through the inspection process.
Here’s what you should check:
- Fluid levels (oil, coolant, hydraulic fluids)
- Tire or track conditions
- Brakes, lights, and signals
- Hoses and belts for signs of wear
- Any unusual noises, leaks, or warning lights
These pre-operation checks don’t have to be lengthy, but they are crucial in preventing equipment failure on the job. It’s about catching small issues before they snowball into bigger problems.
3. Invest in Telematics and GPS Tracking
In today’s digital age, construction managers like you have powerful tools at your disposal. Telematics systems and GPS tracking can help you monitor your equipment in real-time. These tools provide detailed information about equipment usage, performance, and location, which allows you to make informed decisions about maintenance.
Benefits of using telematics:
- Track Equipment Usage: Telematics helps you track how often and how hard each piece of machinery is being used, so you can adjust your maintenance schedule accordingly.
- Monitor Fuel Consumption: By keeping an eye on fuel usage, you can spot inefficiencies and address any issues that are causing your equipment to burn more fuel than necessary.
- Enable Preventive Maintenance: Telematics systems can alert you to potential issues—like excessive engine hours or overheating—before they lead to breakdowns.
4. Use a Maintenance Checklist
Creating a maintenance checklist for each piece of heavy equipment ensures that nothing gets overlooked during inspections and repairs. The checklist should cover all the major components of the machine and be easy for your team to follow.
Your checklist might include:
- Checking fluid levels and replenishing as necessary
- Inspecting tires, tracks, or undercarriage for wear
- Examining hydraulic hoses for cracks or leaks
- Testing brakes and safety mechanisms
- Cleaning or replacing air filters
Using a checklist simplifies the process and ensures that all critical areas are covered during every inspection.
Download Our Free Fleet Maintenance Resources Now!
5. Train Your Operators on Proper Use and Maintenance
Your equipment is only as good as the people who operate it. If your team doesn’t know how to properly use or care for your machines, even the best maintenance schedule won’t be enough. That’s why it’s essential to invest in training for your operators.
Operator training should include:
- Safe and correct operation of each piece of equipment
- Recognizing early warning signs of equipment failure
- How to conduct basic maintenance tasks, like checking fluids or cleaning filters
- Understanding the importance of reporting any issues immediately
By empowering your operators with the knowledge and skills they need, you can reduce wear and tear and prevent accidents on the job.
6. Stay on Top of Documentation
Keeping detailed records of your equipment’s maintenance history can be a game-changer. These records help you track when the last service was performed, what issues were addressed, and when the next maintenance task is due.
Key documentation to maintain:
- Maintenance logs
- Repair history
- Inspection reports
- Parts replacements
- Warranties and service contracts
Having all this information at your fingertips can help you plan future maintenance and make informed decisions about whether it’s time to repair or replace equipment.
Common Mistakes in Heavy Equipment Maintenance and How to Avoid Them
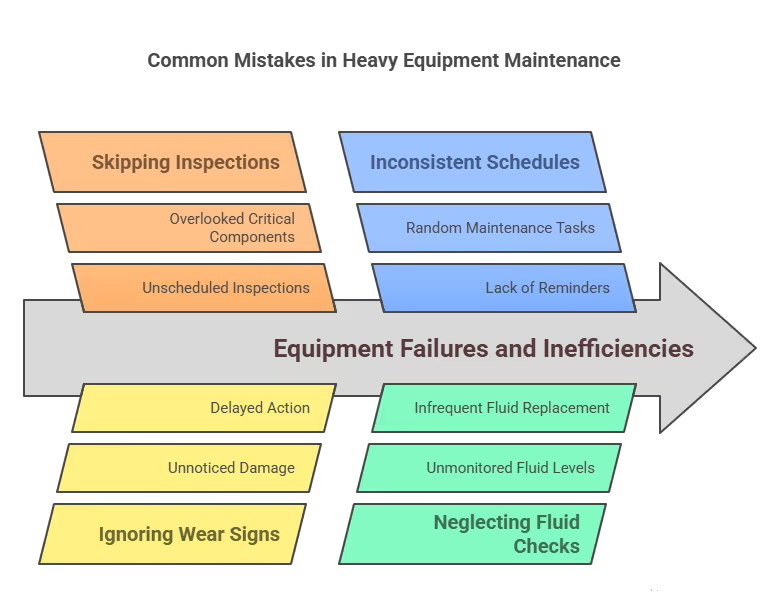
Skipping Regular Inspections:
- Mistake: Skipping routine inspections can lead to unnoticed wear and tear, resulting in sudden equipment failures.
- Solution: Make inspections a regular part of your heavy equipment maintenance checklist. Inspect critical components like engines, tires, and hydraulics at scheduled intervals to catch issues early.
Ignoring Signs of Wear and Tear:
- Mistake: Ignoring visible signs of damage, such as cracks, leaks, or unusual noises, can lead to more serious problems.
- Solution: Train staff to recognize early warning signs of wear and tear and act promptly. Replace worn-out parts before they cause breakdowns.
Inconsistent Maintenance Schedules:
- Mistake: Not following a consistent maintenance schedule or performing maintenance tasks randomly can lead to uneven equipment care.
- Solution: Implement a strict maintenance schedule and stick to it. Use reminders or maintenance management software to track and schedule tasks consistently.
Neglecting Fluid Checks:
- Mistake: Failing to monitor oil and hydraulic fluid levels can cause overheating or system malfunctions.
- Solution: Regularly check fluid levels and replace fluids as needed. This helps ensure smooth equipment operation and prevents damage.
Lack of Detailed Maintenance Records:
- Mistake: Not keeping detailed records of maintenance activities can make it difficult to track when parts were last replaced or serviced.
- Solution: Keep accurate logs of all maintenance tasks. This not only helps track the performance of equipment but also aids in future decision-making for preventive maintenance for heavy machinery.
By avoiding these common mistakes, construction managers can improve equipment performance, prevent costly repairs, and ensure smooth operations.
Related Posts
- Heavy Equipment Inspection: What are the Best Practices for Construction Managers?
- Deciding When to Repair Vs. Replace Heavy Equipment
- Identifying and Resolving Common Maintenance Issues for Heavy Equipment in Construction
- How to Perform Heavy Equipment Inspection the Right Way
Turn Maintenance into an Advantage
Heavy equipment maintenance might seem like just another responsibility on your already long to-do list, but it’s a critical part of running a successful construction business. By staying proactive, setting up regular inspections, and using tools like telematics, you can keep your fleet running efficiently and avoid costly breakdowns.
When you stay on top of maintenance, you reduce downtime, cut repair costs, and extend the life of your machinery. In the long run, this means smoother operations, safer job sites, and less stress for you. So, take charge of your equipment maintenance today, and watch your projects run more smoothly than ever.
Simply Fleet’s Fleet Management software is the perfect solution! With real-time GPS tracking, automated maintenance reminders, fuel consumption monitoring, and detailed reports, you’ll have everything you need to keep your equipment running smoothly. Reduce downtime, cut repair costs, and streamline operations all from one easy-to-use platform. Whether you manage a small or large fleet, Simply Fleet makes it simple to stay on top of your heavy equipment. Try Simply Fleet today and experience hassle-free fleet management! Sign up now!