Key Takeaways
In today's fast-paced world, equipment is crucial for the success and productivity of organizations in industries like construction, landscaping, and farming. Regular maintenance is essential to ensure smooth operation and extend the lifespan of equipment.
Central to an effective equipment maintenance strategy is the equipment maintenance log. This log serves as a comprehensive record-keeping system, capturing important maintenance information such as equipment upkeep records and machinery maintenance documentation. It helps track equipment history using a maintenance tracking system, ensuring businesses stay on top of scheduled equipment servicing and preventive maintenance records.
By maintaining an asset maintenance log or a well-structured maintenance logbook template, organizations can efficiently monitor machine repair logs and operational equipment maintenance. These practices not only support seamless workflows but also enhance the reliability and longevity of essential machinery.
What is an Equipment Maintenance Log?
An equipment maintenance log is a systematic and organized document that records detailed information about maintenance procedures for specific equipment. It acts as a centralized repository for all maintenance data, including routine inspections, equipment upkeep records, machine repair logs, servicing schedules, and other relevant activities.
The primary purpose of an equipment maintenance log is to establish a comprehensive record of all maintenance tasks performed on each piece of equipment. This includes details such as the date and time of maintenance, specific activities conducted, personnel involved, parts or materials used, and any observations or issues identified during the maintenance process. By maintaining preventive maintenance records and utilizing a maintenance tracking system, businesses can ensure operational equipment maintenance is conducted efficiently, reducing downtime and extending the equipment's lifespan.
The 5 Essential Components of Equipment Repair Log
An equipment maintenance log is one of the key documents you need to track the conditions and service history of your equipment. Here are the five main components of an effective equipment maintenance log:
1. Equipment Identification
The equipment identification covers a couple of main topics about the particular types of equipment you’re using. These key details include:
- Equipment Name: It is a unique tag (Delivery Truck #123, Generator A). The equipment name provides easier identification.
- Serial Number: It shows a unique number or post-manufacture code related to equipment.
- Model Number: It is the particular model type of the machine.
- Manufacturer: The manufacturing company that made that equipment.
- Location: It refers to the site of equipment's location.
2. Maintenance Details
Now, let’s discuss the maintenance actions performed on the equipment.
- Date and Time: It is the time of conduction of service or inspection.
- Maintenance Type: The kind of maintenance (e.g. Routine Inspection, Oil Change, Repair) performed.
- Description of Work Order: A professional overview explaining clearly and concisely the tasks performed by the maintenance personnel.
- Maintenance Technician: The name of the person who performed the maintenance service.
3. Inspection and Condition
This section requires the function of a basic analysis and that it provides diagnosis results acquired during the maintenance operations. Key elements include:
- Inspection Findings: Staff conducted recognized Equipment Condition Tests.
- Parts Replaced: They are the listed items of any changed parts during the repair.
- Notes: Comments on the performance of the equipment maintenance.
4. Preventive Maintenance Schedule
Here you are planning for your future maintenance needs to maintenance, making your equipment to be downtime free, and reducing maintenance/repair costs.
It may include:
- Recommended Maintenance Schedule: This could appear as the recommendations of the manufacturer. However, it can also be your plan within your service intervals.
- Next Maintenance Due: An explicit notice regarding the forecasted date of the next routine visit.
- Reminders: Alerts or messages to remind users about planned corrective maintenance works at priority.
5. Additional Information
It gives you a chance to personalize it to fit your unique and personal requirements. You can include:
- Photos/Videos: It may contain a visual record of the equipment's repair. Also, it can showcase the current actual condition of the equipment.
- Meter Readings: Track the hours of operation by withdrawals and other relevant use information.
- Warranty Information: Warranty coverage is specific to the newly ordered equipment.
Types of Maintenance Logs
There are 3 types of maintenance logs. Each form of equipment maintenance log serves a distinct purpose and addresses specific aspects of maintaining equipment. Businesses can select one or combine multiple logs depending on their maintenance needs, industry standards, and equipment complexity.
1. Maintenance Schedule Logs
Maintenance schedule logs are vital for organizing planned and recurring maintenance tasks. These logs provide a structured system for scheduling routine inspections, preventive maintenance activities, and scheduled equipment servicing.
By documenting maintenance schedules, businesses can maintain an efficient maintenance tracking system, reduce the risk of unexpected failures, and ensure consistent operational equipment maintenance. This proactive approach helps extend equipment lifespan and ensures machinery maintenance documentation is accurate and comprehensive.
2. Project Logs
Project Logs focus on capturing maintenance activities related to specific projects or major repairs. These types of equipment repair logs document the timeline, resources allocated, tasks performed, and challenges encountered during the project.
Project Logs provide a comprehensive overview of the maintenance activities undertaken for a particular project, facilitating project management and ensuring effective coordination among team members.
3. Machinery Maintenance Logs
Machinery maintenance logs specifically track maintenance activities for machinery and heavy equipment. These logs are commonly useful in industries such as manufacturing, construction, and agriculture.
They record details about equipment inspections, lubrication, repairs, replacements, and other maintenance tasks. Machinery Maintenance Logs help monitor the health and performance of machinery, identify potential issues, and optimize equipment uptime and longevity.
Importance of Equipment Maintenance Record-keeping for Your Business
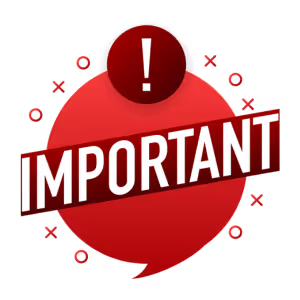
Keeping track of equipment maintenance is crucial for the smooth maintenance workflows of any fleet business. An equipment maintenance log is a detailed record of all maintenance activities performed on a piece of equipment.
It includes information such as the maintenance date, the type of maintenance performed, and the name of the maintenance manager and technician who conducted the maintenance. Let’s see how
1. Track Equipment Maintenance History
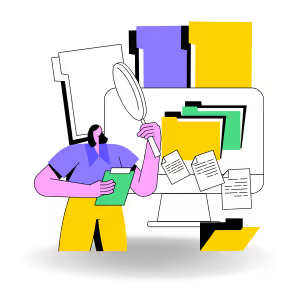
An Equipment Maintenance Log serves as a comprehensive record of all maintenance activities performed on each piece of equipment. It captures crucial details such as dates of maintenance, tasks performed, parts replaced, and personnel involved.
This historical data helps track the maintenance history of equipment, enabling maintenance teams to identify patterns, recurring issues, and equipment performance trends. With this information, they can proactively plan corrective maintenance schedules, identify potential problems, and take preventive measures to avoid costly breakdowns.
2. Preventive Maintenance
Regular maintenance is essential for preventing equipment breakdowns and ensuring that your equipment operates at peak efficiency. You can easily track due maintenance and ensure its on-time maintenance performance. Keeping a maintenance log will help you out in this complex task. This can help prevent costly repairs and unplanned downtime caused by unexpected equipment breakdowns, empowering you to save money.
3. Facilitate Troubleshooting and Repairs
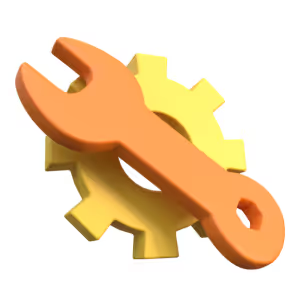
In the event of equipment failure or malfunction, the Equipment Maintenance Log is an invaluable resource for troubleshooting and repairs. The log contains detailed records of past maintenance activities, including identified issues and the solutions applied.
Maintenance teams can refer to these records to quickly diagnose problems, identify potential root causes, and apply appropriate remedies based on past experiences. This approach significantly reduces repair time, minimizing downtime and disruption to operations.
4. Enhance Equipment Reliability and Performance
Regular maintenance, documented in an Equipment Maintenance Log, plays a key role in maintaining equipment reliability and ensuring consistent performance. By adhering to scheduled inspections, lubrication routines, and other preventive maintenance tasks, organizations can keep equipment functioning at its best.
These logs help businesses adopt a systematic approach to maintenance tracking, minimizing wear and tear, and preserving the operational lifespan of assets. A well-maintained logbook template ensures machine repair logs are complete, supporting ongoing operational efficiency.
5. Regulatory Compliance
In industries such as construction, agriculture, and manufacturing, strict regulations often govern equipment maintenance and safety standards. Maintaining detailed equipment service logs allows organizations to demonstrate compliance during inspections and audits, reducing the risk of penalties or legal complications.
Why detailed maintenance logs matter:
- Meeting regulatory requirements with preventive maintenance records.
- Demonstrating a strong commitment to workplace safety.
- Avoiding fines and ensuring adherence to industry standards.
This approach not only promotes safety and compliance but also reinforces a culture of accountability and professionalism in managing operational equipment maintenance.
How to Create an Equipment Maintenance Log?
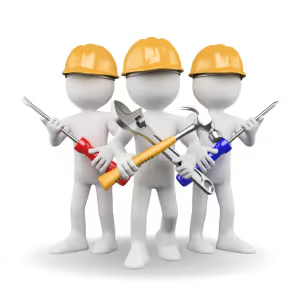
To create an efficient and user-friendly log, it's essential to consider the following steps to create an effective Equipment Maintenance Log.
1. Determine the Required Equipment Information
Begin by deciding the effective equipment maintenance strategy and identifying the specific details to capture in your log. This typically includes the equipment's unique identifier, date and time of maintenance, tasks performed, parts or materials used, personnel involved, and any observations or issues discovered during the maintenance process.
Tailor the log to meet the specific needs and requirements of your organization and industry.
2. Choose a Log Format
Select a format that suits your organizational preferences and ease of use. Options include digital heavy equipment maintenance spreadsheets, digital equipment maintenance management programs, or even physical logbooks.
Ensure that the chosen format allows for easy entry and retrieval of information, and consider accessibility for multiple users if necessary.
3. Establish a Clear Log Structure
Organize your Equipment Maintenance Log logically and systematically. Create columns or fields for each relevant piece of information, providing consistency throughout the log. Clearly label each column and consider using drop-down menus or predefined options for standardization where applicable.
4. Set Up Categories and Equipment Identification
Divide your log into categories based on equipment types, departments, or any other relevant classification. Assign a unique identifier to each piece of equipment to easily differentiate between them. This ensures clarity and facilitates efficient searching and filtering when accessing specific equipment records.
5. Define Maintenance Tasks and Frequency
Establish a list of maintenance tasks that are relevant to each equipment type. Include routine inspections, lubrication, calibration, repairs, and any other necessary tasks. Determine the frequency of task performance and note it in the equipment maintenance log. This helps in creating a maintenance schedule and also ensures consideration of all critical maintenance tasks.
6. Provide Space for Maintenance Personnel
Allocate a dedicated section within the log for users to add notes and observations. This allows maintenance personnel to document any abnormalities, potential issues, or recommendations for future maintenance. Encourage detailed and descriptive entries to provide a comprehensive picture of each maintenance activity.
7. Train and Involve Maintenance Personnel
Provide proper training to maintenance personnel on how to effectively use the Equipment Maintenance Log. Emphasize the importance of accurate and timely data entry. Encourage collaboration and communication among team members. It will ensure regular updation of the equipment maintenance log and reflect the most up-to-date information.
8. Regular Log Review and Improve
Periodically review the effectiveness of your Equipment Maintenance Log and gather feedback from maintenance personnel. Identify any areas of improvement, such as additional fields, streamlined processes, or enhanced accessibility. Continuously refine and adapt the log to meet evolving maintenance needs and technological advancements.
Download Our Free Fleet Maintenance Resources Now
Common Mistakes to Avoid in Maintenance Logs
Even with the best intentions, mistakes can creep into your maintenance logs if you're not paying attention. Here are a few things to keep an eye on:
- Inconsistent Entries: Skipping entries or missing repairs can make the log unreliable. It’s like trying to keep track of your goals without writing them down—you lose the sense of progress.
- Overlooking Digital Options: While paper logs may feel familiar, digital logs provide more efficient tracking and easy access. Don’t miss out on tools that could simplify the process!
- Failure to Review: Writing in a log is just one part of the process; reviewing it regularly is key. Look for recurring issues and adjust maintenance schedules or practices as needed. That part that keeps breaking might need more attention than you think.
The Role of Technology in Equipment Maintenance Logs
Let’s talk about the role of technology in modern maintenance logs. Digital tools are making equipment maintenance management easier and more effective. With features like automatic reminders, cloud-based storage, and user-friendly interfaces, it’s never been simpler to track and review maintenance records.
Think of it like switching from a paper map to GPS—far more convenient and accurate! From simple spreadsheets to comprehensive maintenance management systems (CMMS), digital tools can help you quickly access past logs, spot patterns, and track costs. Plus, real-time notifications for upcoming maintenance mean you're always on top of things.
Equipment Maintenance Log Template: Free Download
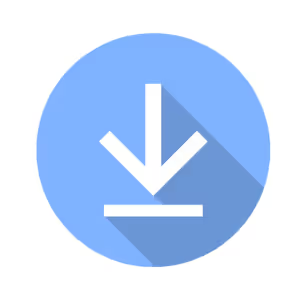
To assist organizations in creating an effective Equipment Maintenance Log, Simply Fleet offers a free downloadable template. This service maintenance record template provides a structured format to capture essential maintenance information, track equipment history, and ensure optimal performance.
Transitioning from Manual to Digital Maintenance Logs
Transitioning from manual to digital fleet equipment maintenance logs offers numerous benefits and is becoming increasingly essential in modern maintenance management. This section explores the advantages of digital logs, guides you on selecting appropriate solutions, outlines the implementation process, and addresses common challenges.
Advantages of Digital Maintenance Logs
Digital equipment maintenance logs streamline the equipment maintenance record-keeping process, improving accuracy and efficiency. They enable real-time data entry and access, reduce human errors, and provide a flexible maintenance dashboard, which is more organized than paper records.
Additionally, equipment maintenance log apps often include analytical tools that help identify trends and optimize maintenance schedules, leading to reduced equipment downtime and better asset maintenance management.
Selecting the Right Digital Solution
Choosing the right maintenance log software is crucial when transitioning to digital maintenance logs. Fleet maintenance software (FMS) with an equipment maintenance log app is a popular choice.
These tools should be user-friendly, integrate well with existing systems, and offer features like automated reminders, real-time data updates, and secure cloud storage. Evaluating different FMS options based on company size, budget, and specific needs will help in making the best choice.
Implementation Steps and Best Practices
- Assessment and Planning: Start by assessing current maintenance best practices and identifying areas for improvement. Develop a clear plan for the transition, including timelines and responsibilities.
- Data Migration: Transfer existing maintenance records from paper to the digital system. This may involve scanning documents and manually entering data.
- Training: Ensure all relevant personnel are trained on the new maintenance tracking system, covering data entry, system navigation, and troubleshooting.
- Pilot Testing: Conduct a pilot test to identify any issues and make necessary adjustments before full-scale implementation.
- Full Deployment and Review: Roll out the system across the organization and regularly review its performance. Gather feedback from users and continuously refine the system.
Overcoming Common Challenges
Common challenges in transitioning to digital logs include resistance to change, data migration complexities, and the learning curve associated with new technology. To address these, involve staff early in the process, provide adequate training, and offer ongoing support. Additionally, ensure data accuracy during migration and address any technical issues promptly.
Related Posts
- Maintenance Log Software: Streamlining Operations and Enhancing Efficiency
- Streamlining Maintenance Tasks: The Power of Work Order Management Software
- Maximize Uptime for Your Earth-moving Heavy Equipment: Preventative Maintenance Tips
Final Words
In the realm of equipment maintenance, having a well-maintained and organized Equipment Maintenance Log can make all the difference. It provides a treasure trove of information, enabling organizations to track maintenance activities, plan scheduled machine maintenance, troubleshoot problems, and optimize equipment performance. So, commit to implementing and maintaining an Equipment Maintenance Log, and reap the rewards of a well-maintained and high-performing equipment fleet.