Have you ever wondered how a vast, empty plot of land transforms into a construction site? The answer lies in the titans of the industry: earthmoving construction equipment.
β
These mechanical marvels are the muscle behind every build, forging the way for the structures that take shape. From carving out foundations to meticulously grading surfaces, earthmoving equipment plays a critical role in the ballet of construction.
β
What are the Earthmoving Construction Equipments?
β
Earthmoving construction equipment forms a kind of heavy machinery that is useful for heavy lifting, site clearing, digging, loading, hauling, grading, and leveling of the surface. This eventually helps get a site ready for the building process.
β
Let's look into the functionalities of some of the most prominent earthmoving equipment:
β
Excavators:
β
The defining characteristic of excavators is a hydraulic arm with a boom and bucket attachment. This configuration allows them to excel at various digging tasks, including trenching for utilities, foundations, or drainage systems. They can handle large-scale excavations for basements, ponds, or even demolition projects when equipped with the appropriate attachments.
β
Bulldozers (Dozers):
β
Bulldozers consist of large, robust blades at the front side. They help push substantial debris for preliminary leveling and clearing vegetation. It also provides for stockpiling of soil or other materials for later use.
β
Bulldozers possess the power to break up hard or compacted soil. It makes them ideal for preparing the ground for further excavation.
β
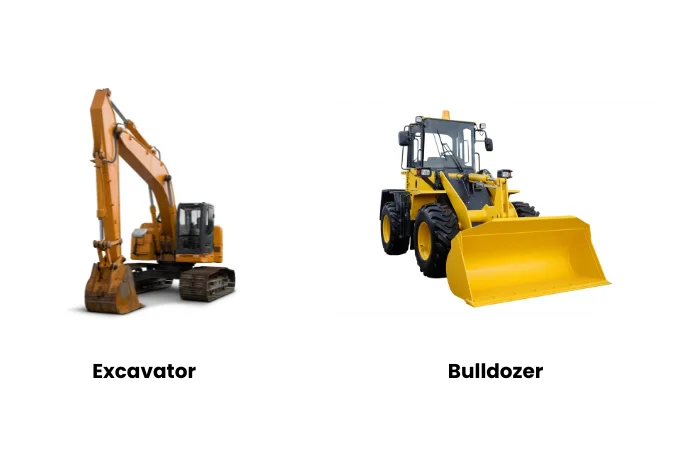
β
Loaders:
β
The loaderβs primary function is to utilize the large front bucket to load loose materials into dump trucks. This includes materials like dirt, gravel, or sand.
β
They can be further equipped with pallet forks or other specialized attachments to handle a diverse range of materials, like bricks, pipes, or lumber. They play a vital role in site clean-up, removing debris, or stockpiling excavated materials throughout the construction process.
β
Dump Trucks:
β
As the essential haulers of any construction site, dump trucks are designed for a singular primary function: transporting loose materials. These large, sturdy trucks efficiently haul dirt, gravel, sand, or demolition debris from the excavation site to designated disposal areas.
β
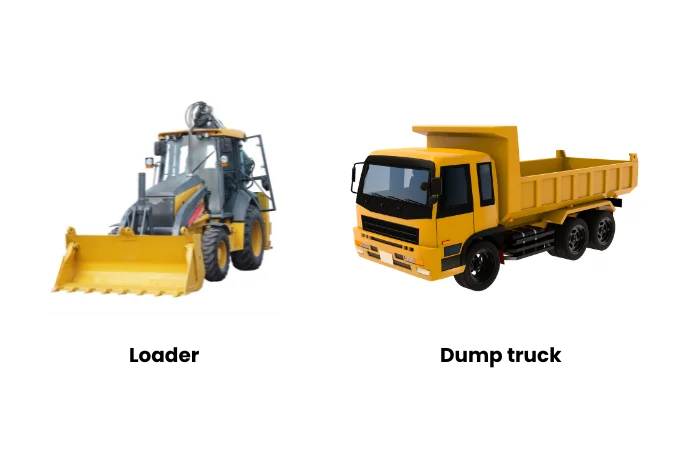
β
Backhoe Loaders:
β
These machines offer a unique combination of excavator and loader functionalities. They provide digging capabilities through a backhoe attachment that allows for trenching or foundation work. The front loader bucket caters to efficient scooping and loading of loose materials.
β
Graders:
β
Equipped with a long extendable blade, graders meticulously scrape and level the ground to achieve a precise design grade for foundations or other structures. These heavy-duty machines can also create specific slopes for drainage or other design requirements.
β
From Reactive Repairs to Proactive Protection: Earthmoving PM Plans
β
Preventive maintenance is not just about fixing problems; it's about avoiding them altogether. For earthmoving equipment, a preventive maintenance approach offers a multitude of benefits that translate into significant advantages for your construction projects.
β
Reduced Downtime
β
Earthmoving equipment works tirelessly, battling harsh conditions and enduring heavy workloads. Unscheduled breakdowns can cripple project timelines, leading to delays, missed deadlines, and potential penalties.
β
However, preventive maintenance acts as a shield, identifying and addressing minor issues before they escalate into major failures. This proactive approach ensures your earthmoving equipment remains operational and your construction project stays on schedule.
β
Extending the Lifespan of Your Equipment
β
By adhering to manufacturer-recommended maintenance schedules, lubricating critical components, and replacing worn-out parts before they cause damage, you ensure your equipment operates efficiently and experiences minimal wear and tear.
β
This translates into a longer lifespan for your earthmoving fleet, allowing you to reap the benefits of your investment for a longer period.
β
Optimizing Costs and Saving Money in the Long Run
β
While preventive maintenance may seem like an upfront cost, it's a strategic investment that saves money in the long run. Catching minor problems early prevents them from escalating into expensive repairs.
β
Regular maintenance extends the lifespan of your equipment, reducing the need for premature replacements. Additionally, well-maintained equipment operates more efficiently, consuming less fuel and minimizing operating and repair costs.
By adopting a proactive approach to preventive maintenance, you optimize your equipment's performance and meet project deadlines on time, avoiding inflated project costs.
β
Prioritizing Safety on the Job Site
β
Construction sites can be inherently hazardous environments. Equipment failures pose a significant risk to workers' safety. Preventive maintenance plays a crucial role in mitigating these risks while adhering to the OSHA compliance guidelines. Whereas, regular inspections can also identify potential safety hazards like loose components, fluid leaks, or faulty brakes before they lead to accidents.
β
Ensuring proper tire inflation and replacing worn-out treads improves traction and handling, minimizing the risk of rollovers or accidents. By prioritizing preventive maintenance, you create a safer work environment for your crew, fostering a culture of safety on the job site.
β
Understanding the Scope of Earthmoving Equipment Maintenance
β
Earthmoving equipment operates in a harsh environment. They're constantly exposed to dirt, dust, extreme temperatures, and heavy workloads. A proactive maintenance approach is essential to ensure these machines perform reliably and avoid costly breakdowns.
β
Here's a comprehensive breakdown of the key earthmoving equipment maintenance needs, categorized by task:
β
1. Fluid Management:
β
Fluids are the lifeblood of earthmoving equipment, playing a crucial role in lubrication, cooling, and power transmission. Here's what you need to consider:
β
- Engine Oil: Regular oil changes are vital to maintain engine performance and prevent wear and tear. Oil analysis can be performed to identify potential engine issues early on.
- Hydraulic Fluid: Hydraulic systems power various excavator and loader functions. Hydraulic fluid testing is crucial to ensure it remains clean and free of contaminants that could damage components.
- Coolant: Coolant regulates engine temperature. Coolant level checks and top-ups are essential to prevent overheating, which can lead to severe engine damage.
- Greasing: Regular greasing of critical components like pins, bushings, and joints minimizes friction and reduces wear. Grease points should be identified and lubricated according to the manufacturer's recommendations.
β
2. Filter Maintenance:
β
Filters play a critical role in keeping fluids clean and protecting essential components from contaminants. Here are the key filters to consider:
β
- Air Filters: Clean air filters ensure optimal engine performance and fuel efficiency. Regularly scheduled replacements are essential to prevent clogged filters from restricting airflow and reducing engine power.
- Oil Filters: Oil filters trap contaminants within the engine oil. Oil filter changes should be performed during oil changes to ensure clean oil circulates through the engine.
- Fuel Filters: Fuel filters prevent dirt and debris from entering the engine's fuel system, which can cause performance issues or breakdowns. Fuel filter replacements should be performed according to the manufacturer's earthmoving maintenance schedule.
β
3. Regular Inspections:
β
Visual inspections are a vital preventative maintenance practice. Here's what to do to inspect your tools and equipment:
β
- Leaks: Inspect for leaks of fluids like engine oil, hydraulic fluid, or coolant. Leaks can indicate worn seals or damaged components and should be addressed promptly.
- Loose Components: Check for loose bolts, nuts, or other fasteners. Loose components can vibrate and cause further damage if not tightened.
- Worn-Out Parts: Visually inspect belts, hoses, and moving parts like tires for signs of wear and tear, cracking, or dry rot. Replacing worn-out parts before failure prevents downtime and potential safety hazards.
β
4. Preventive Maintenance Scheduling:
β
Certain components within earthmoving equipment have specific lifespans and require replacement at scheduled intervals as outlined in the manufacturer's maintenance manual.
β
Examples include:
β
- Belts and Hoses: Rubber belts and hoses deteriorate over time and can crack or snap, potentially causing leaks or complete system failure. Replacing them at recommended intervals ensures optimal performance and prevents breakdowns.
- Tires: Worn-out tires can impact traction, handling, and fuel efficiency. Regularly monitoring tire tread depth and replacing them when necessary is crucial for safety and performance.
- Batteries: Batteries have a limited lifespan and can lose their ability to hold a charge. Scheduled battery replacements prevent starting issues and ensure reliable construction equipment operation and maintenance.
β
Implementing a comprehensive program for the maintenance of construction equipment is very essential. It can help your earthmoving equipment operate smoothly, minimize downtime, and extend the lifespan of your valuable machinery.
β
Download Our Equipment Maintenance Resources Now!
6 Powerful Tips for Effective Earthmoving Equipment Maintenance
β
Maximizing the uptime of earthmoving construction equipment and ensuring their smooth operation is crucial for any project's success. Preventive maintenance (PM) is your key solution in this battle against downtime and unexpected breakdowns.
β
But how do you achieve truly effective preventive maintenance for your earthmoving fleet? Here are 6 powerful tips to ensure the same:
β
1. Make a Construction Equipment Maintenance Plan
β
The foundation of effective preventive maintenance lies in a well-defined maintenance plan. This roadmap should detail the specific maintenance tasks required for each piece of equipment in your fleet. Refer to manufacturer recommendations and consider your equipment usage patterns. For instance, heavily used excavators might require more frequent inspections of hydraulic systems than a less frequently used dozer.
β
The construction equipment maintenance checklist and plan should also outline the frequency of each maintenance task. For example, daily, weekly, monthly, or annually. Assign responsible personnel for each task, ensuring clear accountability within your team.
β
2. Scheduling Regular Inspections
β
Effective earth-moving equipment maintenance is not a one-time event; it's a continuous process. It is important to schedule regular inspections as per your heavy equipment maintenance checklist.
β
These inspections can be categorized into various frequencies:
β
- Daily Inspections: Encourage machine operators to perform quick visual checks before starting their shift, looking for leaks, loose components, and unusual conditions.
- Weekly Inspections: These more detailed inspections may involve checking fluid levels, filter conditions, and the basic functionality of various systems.
- Monthly Inspections: Schedule more comprehensive inspections, potentially involving greasing specific components and tightening bolts as needed.
- Annual Inspections: These in-depth inspections may involve a thorough examination by qualified technicians, potentially including oil analysis and detailed assessments of critical systems.
β
3. Empowering Your Operators
β
Your equipment operators are on the front lines, spending the most time with your earthmoving machines. Provide them with proper training on basic maintenance tasks. For example, checking fluid levels, recognizing warning signs like unusual noises or vibrations, and reporting any potential issues promptly.
β
Empowering your operators to identify potential problems early on can prevent minor issues from escalating into major breakdowns. Regular operator training sessions on the maintenance of heavy earth-moving equipment can significantly contribute to the overall effectiveness of your PM program.
β
4. Keeping Detailed Maintenance Records
β
Maintain a detailed earthmoving equipment maintenance log for each piece of equipment in your fleet. This maintenance sheet or log should record the date, type of maintenance performed, parts replaced, and any observations made by technicians.
β
These detailed records offer a wealth of historical data. Identify trends in maintenance needs and earth-moving equipment repairs. They can help you refine your PM program and predict potential issues before they occur.
β
5. Invest in Smart Tools
β
Modern technology offers valuable tools to enhance your PM efforts. Consider investing in preventative maintenance tools such as:
β
- Oil Analysis Kits: These kits allow you to analyze engine oil samples and identify potential internal engine wear or contamination before major problems arise.
- Vibration Analysis Tools: Vibrations can indicate potential issues with bearings or other components. Vibration analysis tools can help detect these issues early on, preventing costly repairs.
β
6. Leverage Fleet Maintenance Software
β
Construction equipment maintenance software plays a crucial role in managing the maintenance needs of your earthmoving fleet. Here's how it helps:
β
- Streamlined scheduling maintenance: Schedule tasks, set reminders, and track maintenance history for each equipment piece.
- Simplifies record keeping: Electronically store maintenance records, reports, and inspection data for easy access and analysis.
- Improves communication: Facilitates communication between maintenance crews, operators, and fleet managers.
- Provides data-driven insights: Use the fleet maintenance system to analyze maintenance data and identify trends that can help you optimize your maintenance program. For instance, you can get real-time fault codes with the help of a telematics feature.
β
The Way Ahead
β
By implementing these six powerful tips along with the application of construction fleet maintenance software, you can transform your earthmoving equipment maintenance program from reactive to proactive.
β
Building a culture of preventative maintenance within your organization will ensure your equipment operates at peak performance, maximize uptime, and extends its lifespan. This translates into maximized project efficiency and cost savings in the long run. So, take charge of your equipment's health, and watch your construction projects gear to long-term success.