Managing a fleet is no easy job. You’re constantly juggling schedules, vehicle maintenance, fuel costs, driver safety, and meeting delivery deadlines. Now, add ineffective spare parts inventory management to the mix, and things can get even more chaotic. One minute, you’re trying to get a vehicle back on the road, and the next, you find out the part you need is out of stock—or worse, back-ordered for weeks. Suddenly, what could have been a quick repair turned into extended downtime, disappointed customers, and unexpected expenses.
If that sounds familiar, you’re not alone. Many fleet managers struggle with keeping spare parts organized and available when needed. But the good news is, you can get ahead of this problem. By taking control of your spare parts inventory, you’ll be able to keep your vehicles on the road longer, reduce repair times, and save your business both time and money.
In this article, we’ll walk you through simple, actionable steps to help you manage your fleet’s spare parts inventory like a pro, eliminating common headaches that come with it.
Why is Managing Spare Parts Inventory Such a Big Deal?
Let’s face it—your fleet is only as reliable as the parts that keep it running. When a vehicle breaks down or requires maintenance, having the right part on hand can mean the difference between getting back on the road in hours or sitting idle for days, if not weeks. And downtime? That’s where the real pain hits. Every minute one of your vehicles isn’t operational, your company is losing money. Unplanned downtime can lead to missed deliveries, frustrated customers, and even penalties, depending on the industry you’re in.
On the other hand, keeping too many spare parts can tie up capital in unnecessary stock. You’re essentially sitting on money that could be better spent elsewhere in your business. Overstocking also means higher storage costs and the risk of parts becoming obsolete before they’re ever used.
So, the goal here is to find that sweet spot—keeping just the right amount of parts in stock, available when you need them, without going overboard. Sounds easier said than done, right? Don’t worry, we’ll break it down step-by-step.
The Delays in Repairs and Increased Downtime
Have you ever had to deal with the frustration of waiting days or even weeks for a spare part to arrive? Every hour of downtime means lost revenue, and the longer your vehicles are out of service, the bigger the impact on your bottom line. Plus, let’s not forget about the ripple effects: missed deadlines, unhappy customers, and drivers sitting idle.
Simple Tips to Manage Your Fleet’s Spare Parts Inventory
The first step to eliminating these delays is to get a clear understanding of your fleet’s needs. Not all parts are equally essential. Some may be critical and required frequently, while others are rarely used but crucial when needed.
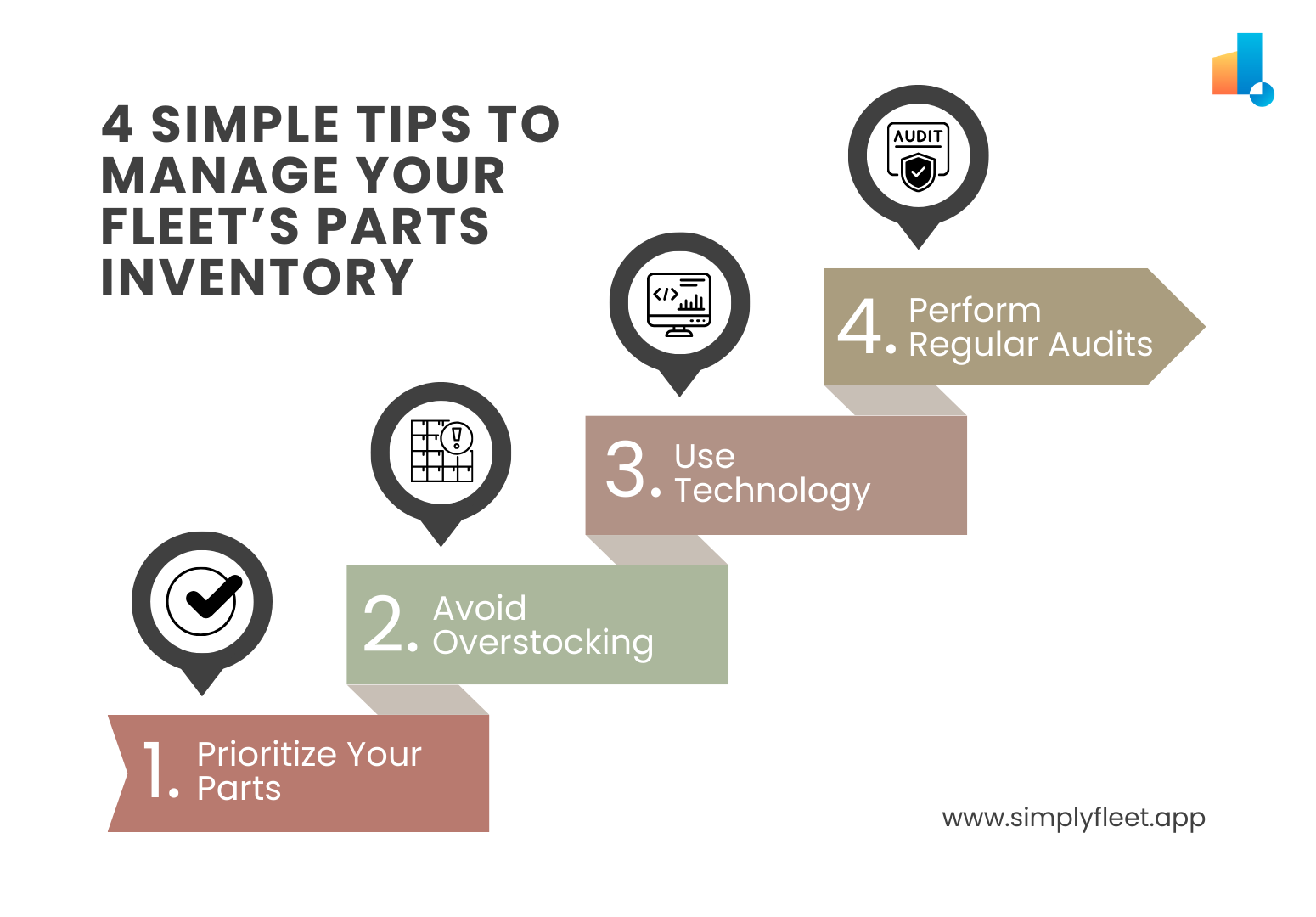
Step 1: Prioritize Your Parts
The first step to effective spare parts inventory management is to figure out which parts are the most critical. Not all vehicle parts are created equal. Some parts wear out more often, and others are essential for keeping your fleet on the road. For instance, parts like brakes, tires, and batteries are high-use items. You’ll likely need these more frequently than less commonly replaced items like engine components or specialized electronics.
Here’s a simple way to classify your parts:
- High-priority parts – These are essential to your fleet’s daily operation. Think of them as “must-haves” because, without them, your vehicles can’t run. Examples include brake pads, filters, or tires.
- Medium-priority parts – These parts don’t wear out as fast but are still important for overall vehicle function. You’ll need to keep some of these on hand but not as many as the high-priority parts.
- Low-priority parts – These parts are rarely needed but can lead to serious downtime if you don’t have them when required. Things like specialized sensors or rare engine components might fall into this category.
Once you’ve classified your parts, you’ll be better equipped to stock the right quantities of each. For high-priority parts, aim to keep enough on hand to cover a couple of emergencies, while for low-priority parts, it may make more sense to order them as needed.
Download Our Free Fleet Inventory Resources Now!
Step 2: Avoid Overstocking and Optimize Inventory
One of the best ways to avoid overstocking is to use a software solution to track inventory in real-time. This kind of system can help you monitor how often each part is used, how many you have left, and alert you when it’s time to reorder.
By tracking your inventory in real-time, you can avoid the common mistake of panic-buying or bulk ordering when it’s not necessary. Instead, you can order parts based on data, ensuring you’re not wasting money on stock that might never get used.
A good system will also help you keep track of which parts are nearing their expiration dates or are becoming obsolete. This ensures you’re not holding onto parts that will no longer be compatible with your vehicles.
Step 3: Use Technology for Inventory Management
Say goodbye to paper logs, Excel sheets, or outdated systems. Implementing fleet management software that integrates spare parts inventory management can save you time, reduce errors, and give you full visibility of your stock.
With an automated system, you’ll:
- Track parts usage – Know exactly how many parts are being used and when.
- Get low stock alerts – Never run out of critical parts again with automated alerts that tell you when to reorder.
- Track costs – Keep an eye on spending and avoid unnecessary purchases.
- Access real-time data – Check inventory from anywhere, whether you’re at the office or on the go.
Step 4: Perform Regular Audits
Even with the best system in place, it’s important to perform regular audits of your spare parts inventory. This ensures that what’s in the system matches what’s on the shelves. A quick weekly or monthly audit can help catch any discrepancies early on before they become costly problems.
Additionally, audits give you a chance to re-evaluate your stock levels. If you find that certain parts are rarely used, you can reduce the number you keep in stock and reallocate those funds to more critical parts.
Related Posts
- Mastering Your Fleet's Parts Inventory in 6 Steps: A Comprehensive Guide
- Essential Features of Equipment Inventory Management Software
- Importance of Efficient Parts Inventory Management
Keep Your Fleet Moving with Simply Fleet’s Smart Inventory Solutions!
Managing your fleet’s spare parts inventory might seem like a daunting task, but by implementing these steps, you can take control of your stock, reduce downtime, and save money in the long run. Prioritize your parts, avoid overstocking, leverage technology, and stay on top of regular audits. By doing this, you’ll be able to manage your spare parts inventory like a pro, keeping your fleet running smoothly and your business growing.
Simply Fleet's Fleet Management software provides real-time tracking, low-stock alerts, and automated reporting, which can help you avoid costly downtime, reduce errors, and optimize your inventory levels effortlessly. Stop wasting time with manual processes and start saving money with smarter inventory management. Try Simply Fleet today and keep your fleet running smoothly and efficiently!