In any industry, the smooth operation of equipment and assets is crucial for maintaining productivity, reducing costs, and boosting return on investment (ROI). One effective way to achieve this is through a well-designed preventive maintenance plan.
β
What is a Preventive Maintenance Plan?
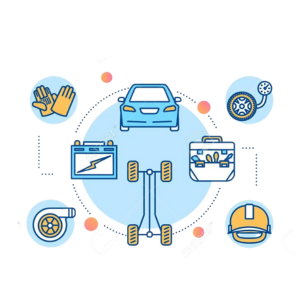
β
A planned preventive maintenance is a proactive approach to equipment and asset management that focuses on scheduled inspections, cleaning, adjustments, and repairs. It aims to prevent unexpected breakdowns, extend asset lifespans, and optimize performance.Β
β
Rather than waiting for equipment failure to occur, preventive maintenance helps organizations stay ahead of potential problems, saving time, money, and resources in the long run.Β
β
Before diving deep into the steps to create a preventive maintenance plan, letβs look at the types of preventive maintenance.Β
β
Types of Preventive MaintenanceΒ
β
Preventive maintenance (PM) for vehicles and equipment encompasses a variety of approaches tailored to address potential issues before they escalate into costly breakdowns.Β
β
Here's a breakdown of the most common types of PM:
β
1. Time-Based Maintenance
β
This is the most traditional type of maintenance. It requires scheduling to perform routine maintenance tasks at a predetermined time.
β
For instance, oil changes have to be undertaken after 3 months and filters have to be replaced within a certain time frame. While some fleet checks are performed based on how long ago it was last done.
β
2. Usage-Based Maintenance
β
This type of PM allows for the performance of maintenance services scheduled according to real-time usage rather than fixed maintenance intervals. Time intervals for these services could be milestones like engine operating hours, mileage for tire rotations, and others, etc.
β
3. Condition-Based Maintenance (CBM)
β
This approach is proactive in nature; it relies on precision monitoring and predicts good outcomes through data analysis to prevent failure. Specific cases comprise the utilization of oil analysis to identify instances of wear, the use of vibration monitoring to detect problems with bearings, etc.
β
4. Predictive Maintenance (PdM)
β
This high-tech approach uses big data analytics and machine learning to detect problematic equipment before they even have breakdowns.
β
This tool makes use of historical maintenance data, sensor data, as well as operating conditions to lead in predicting the occurrence of likely issues and schedules the maintenance to be carried out at the appropriate time.
β
Benefits of Preventive Maintenance
β
β
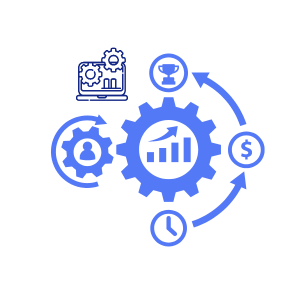
β
Implementing a preventive maintenance plan offers numerous advantages for organizations of all sizes. Here are some key benefits:
β
1. Enhance productivity levels
β
Regular preventive plan maintenance minimizes unexpected breakdowns, ensuring equipment remains operational for longer periods. This reduces unplanned downtime and increases overall productivity.
β
2. Reduce asset downtime
β
Scheduled maintenance allows for planned downtime, eliminating the need for lengthy and costly unscheduled repairs. This results in minimal disruptions to operations and optimized asset utilization. According to a study by the American Society of Quality, preventive maintenance can reduce unplanned downtime by up to 25%.
β
3. Lower expenses
β
β
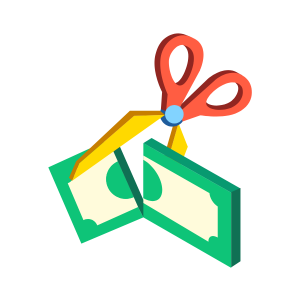
By troubleshooting minor issues before they escalate into major problems, preventive maintenance reduces the need for expensive repairs or equipment replacements. A study by the Society for Maintenance & Reliability Professionals indicates that PM programs can save businesses up to 30% on maintenance costs. Moreover, It also helps organizations avoid potential fines or penalties due to non-compliance.Β
β
4. Emphasize safety measures
β
β
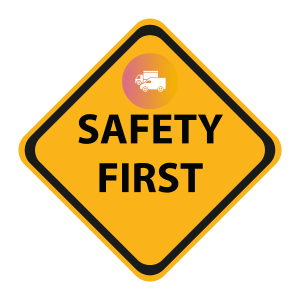
Regular fleet checks and maintenance ensure vehicles operate safely and meet regulatory standards. This helps prevent accidents, injuries, and costly litigation.
β
5. Improve customer satisfaction
β
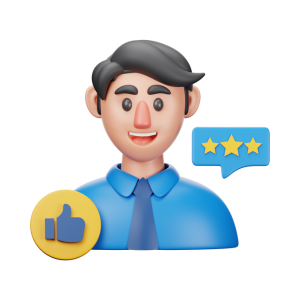
Reliable equipment leads to uninterrupted service delivery, enhanced customer experiences, and improved satisfaction levels. Preventive maintenance plays a vital role in ensuring consistent and high-quality output.
β
Why do Preventive Maintenance Plans Fail?
β
β
β
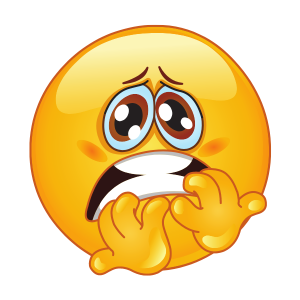
β
Preventive maintenance plans are designed to minimize equipment failures and maximize operational efficiency. However, these plans can sometimes fail due to various reasons.Β
β
Lack of skills
β
One common cause is the failure to provide proper training for maintenance technicians. Without adequate training, technicians may lack the necessary skills and knowledge to effectively execute preventive maintenance tasks, leading to subpar results and potential equipment failures.
β
Poor communication
β
Another factor that can contribute to the failure of preventive maintenance plans is mismanaging oversight, accountability, and transparency.Β
β
When there is a lack of clear roles and responsibilities, as well as poor communication and tracking systems, it becomes challenging to ensure that maintenance tasks are completed as scheduled.Β
β
This can result in missed fleet checks, incomplete maintenance activities, and a lack of accountability within the maintenance team.
β
Undermining root cause analysis
β
Additionally, overlooking the root causes of equipment breakdowns can undermine the effectiveness of preventive maintenance. Simply addressing the symptoms without identifying and addressing the underlying issues can lead to recurring problems.Β
β
It is crucial to conduct thorough root cause analysis to identify factors such as design flaws, operational conditions, or environmental factors that contribute to equipment failures.Β
β
By addressing these root causes, organizations can develop more targeted and effective preventive maintenance strategies.
β
What should a Preventive Maintenance Plan Include?
β
β
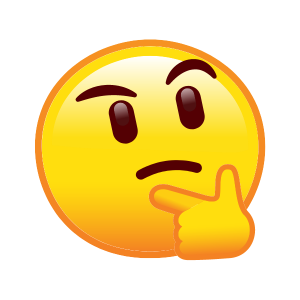
β
To create an effective preventive maintenance plan, several key components must be considered:
β
1. Conduct an inventory of assets
β
Begin by creating an inventory of all the assets that require maintenance. This includes equipment, machinery, vehicles, and any other relevant assets.
β
2. Prioritize assets based on importance
β
Prioritize assets based on criticality, usage frequency, and their impact on operations. This ensures that resources are allocated efficiently and high-priority assets receive periodic maintenance.
β
3. Establish preventive maintenance schedule
β
Develop a comprehensive schedule that outlines maintenance activities for each asset. This includes frequency of inspections, lubrication, calibration, and other preventive tasks.
β
4. Implement a Computerized Maintenance Management System (CMMS) software
β
Utilize computerized maintenance management system (CMMS) software to streamline the preventive maintenance process. These tools help track asset history, and maintenance history logs, schedule maintenance tasks, and generate reports for analysis.
β
5. Enhance team communication and collaboration
β
Establish clear channels of communication between maintenance technicians, supervisors, and other relevant stakeholders. This promotes collaboration, ensures timely task completion, and allows for effective problem-solving.
β
6. Define goals and key performance indicators (KPIs) for the preventive maintenance plan
β
Define specific goals and key performance indicators (KPIs) to measure the effectiveness of the preventive maintenance plan. This enables organizations to track progress and make data-driven decisions.
β
7. Secure support from upper management
β
Gain support from upper management to secure necessary resources, budget, and personnel for implementing and sustaining the preventive maintenance plan. Their buy-in is crucial for the plan's success.
β
How to Make a Preventive Maintenance Plan?
β
A well-defined preventive maintenance program is the backbone of any successful fleet operation. By prioritizing scheduled service and meticulous maintenance planning, you can significantly extend the equipment longevity of your vehicles. This proactive approach minimizes costly downtime by focusing on routine inspections and essential maintenance tasks before problems arise.Β
β
Through established service intervals, you ensure your equipment functions at peak efficiency, maximizing equipment reliability. Investing in preventive maintenance is a smart business decision, shifting your focus from reactive repairs to proactive maintenance, ultimately saving you time and money in the long run.Β
β
Are you ready to put these benefits into action? Let's explore how to make a preventive maintenance plan.
β
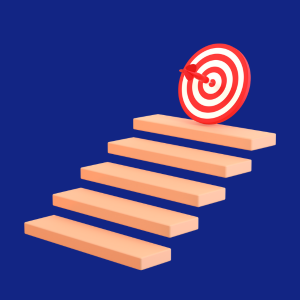
β
To create a solid preventive maintenance plan, follow these eight fundamental steps:
β
1. Develop and prioritize objectives
β
Define the objectives of the plan, such as reducing downtime, improving asset reliability, or optimizing preventive maintenance costs. Prioritize these goals based on their significance to the organization.
β
2. Establish and evaluate key performance indicators (KPIs)
β
Develop KPIs that align with the established goals. These could include metrics like mean time between failures (MTBF), overall equipment effectiveness (OEE), or maintenance cost as a percentage of asset value.
β
3. Obtain support from stakeholders
β
Involve key stakeholders, including maintenance teams, operators, supervisors, and executives, in the planning process. Seek their input, address concerns, and gain their support for successful plan implementation.
β
4. Utilize preventive maintenance software
β
Invest in fleet maintenance tracking software that suits your organization's needs. Ensure it offers features like work order management, asset tracking, maintenance history, and reporting capabilities.
β
5. Implement project management triggers
β
Establish triggers to initiate preventive maintenance tasks based on usage, time intervals, meter readings, or condition-based data. This ensures tasks are executed on time and as required.
β
6. Provide training for maintenance personnel
β
Provide comprehensive training to maintenance technicians on implementing the preventive maintenance plan. This includes understanding maintenance procedures, using the CMMS software effectively, and following safety protocols.
β
7. Develop a comprehensive checklist for preventive maintenance
β
Create a detailed checklist for each asset, outlining the specific tasks, required tools, and safety precautions for each maintenance activity. This ensures consistency and thoroughness in maintenance procedures.
β
8. Refine the preventive plan maintenance based on observed outcomes
β
Regularly analyze the data and reports generated by the CMMS software. Assess the effectiveness of the plan, identify areas for improvement, and make necessary adjustments to optimize the preventive maintenance strategy.
β
Final Words
β
A well-structured preventive maintenance plan is a valuable asset for any organization looking to increase productivity, minimize downtime, reduce costs, promote safety, and enhance customer satisfaction.Β
β
By following the outlined steps and incorporating the essential components, businesses, and fleet managers can create a robust preventive maintenance strategy that ensures the smooth operation of assets, maximizes efficiency, and minimizes disruptions.Β
β
Investing time and resources in Simply Fleet's preventive maintenance solution today will lead to long-term benefits and improved bottom-line performance.
β
β