According to the Bureau of Labor Statistics (BLS), in 2022, there were 1,056 fatal work injuries in the construction industry in the United States. This highlights the critical need for workplace safety, especially in environments where OSHA heavy equipment regulations and hazardous conditions play a major role.Β
β
The Occupational Safety and Health Administration (OSHA) plays a vital role in ensuring worker safety by establishing and enforcing comprehensive regulations.
What are OSHA Compliance Requirements?
β
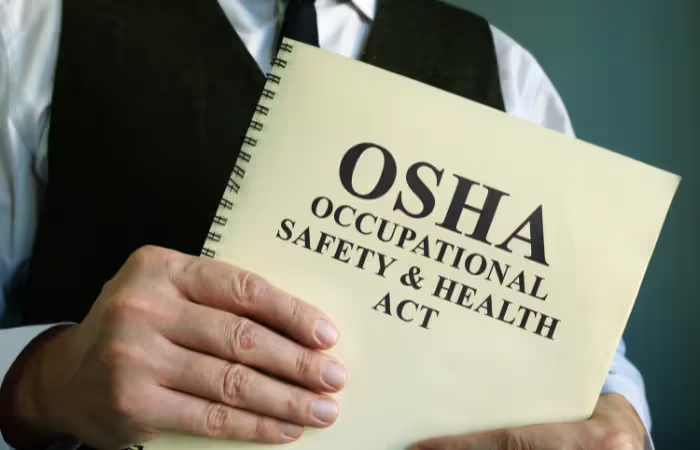
β
What are OSHA Compliance Requirements?
The Occupational Safety and Health Administration (OSHA) is one of the federal agencies that was created within the Department of Labor by the Occupational Safety and Health Act of 1970 (OSH Act).Β
β
OSHA has regulations aimed at maintaining a safe workplace. These regulations apply to all aspects of a construction project, including the vehicles and machinery used. Construction equipment poses unique hazards and risks, so employers must follow OSHA construction standards to protect their employees.Β
β
Essential OSHA Requirements for Construction Equipment
β
OSHA regulations are in place to protect workers and ensure their safety. Thus, employers must take these requirements seriously and implement them effectively. Here are some of the OSHA requirements for construction fleets:
β
Equipment Maintenance:Β
β
Employers must ensure that all construction equipment meets OSHA heavy equipment inspection requirements by keeping it properly maintained and in safe working condition. Regular inspections and maintenance checks should be conducted to identify any potential issues or defects that could affect construction safety compliance. This includes checking brakes, tires, lights, and other essential components.
β
Training and Certification:Β
β
All employees who operate construction vehicles must receive proper safety training and certification.Β As per OSHA 1926.21(b)(2), the employer shall instruct each employee in the recognition and avoidance of unsafe conditions. He has to consider regulations applicable to his work environment to control or eliminate any hazards or other exposure to illness or injury.
β
Load Securement:Β
β
Ensuring that loads are properly secured on construction vehicles is essential for maintaining construction safety compliance and preventing accidents. According to OSHA heavy equipment regulations, various load-securing methods are permitted, including direct tie-downs, indirect tie-downs, and blocking and bracing, all of which help reduce the risk of equipment-related hazards on job sites.
β
Personal Protective Equipment:Β
β
Workers who operate construction equipment should be provided with appropriate personal protective equipment (PPE) to protect them from potential physical and electrical hazards. This may include hard hats, gloves, safety goggles, respiratory protection, and other insulated protective gear.Β
β
Moreover, construction requirement vehicles must be equipped with necessary safety features such as seat belts, roll-over protection, and reflective markings for visibility.
β
Hazard Communication Program (HCP):Β
β
Employers must inform workers about potential workplace hazards related to OSHA heavy equipment and other construction machinery. Clear communication should include guidelines on construction safety equipment, safe operation procedures, and precautions for handling electrical equipment or hazardous chemicals.
β
It should be taken to prevent accidents or injuries. In this way, you can prevent significant fatalities with the help of appropriate hazard communication standards.
β
Emergency Action Plan:Β
β
Employers should have emergency action plans or procedures in place in case of accidents or electric equipment malfunctions. These plans should align with OSHA construction site requirements and include readily available first aid kits, along with clear instructions on responding to emergencies.
β
Documentation:Β
β
Keeping detailed & accurate records of vehicle inspections, maintenance, training, and incidents is essential for demonstrating compliance with OSHA regulations. This documentation should be easily accessible for inspections and regular safety audits.
β
By following these OSHA compliance requirements and the directions given in the video below, employers can create a safer working environment for their employees and reduce the risk of injuries and accidents on the job site.Β
β
Step-by-Step Heavy Equipment Inspection Checklist
Proper heavy equipment inspections are crucial for maintaining OSHA compliance and ensuring worker safety. OSHA heavy equipment inspection requirements mandate that inspections be conducted regularly to identify and address potential hazards before they cause accidents. Below is a structured checklist to guide pre-operation, operational, and post-operation inspections.
β
β
In recent years, OSHA heavy equipment regulations have been updated to strengthen workplace safety and address evolving risks in the construction industry. These changes aim to address potential risks and improve overall safety standards in the construction industry.
β
Focus on Personal Protective Equipment (PPE)
β
One significant update is the introduction of new regulations regarding the use of personal protective equipment (PPE) on construction sites. Workers are now required to use essential PPE, including hard hats, safety glasses, and gloves, to reduce the risk of injuries and comply with OSHA heavy equipment regulations.
β
Employers are responsible for ensuring that their employees have access to the necessary PPE and are trained on how to use it properly.
β
Stricter Inspection and Maintenance Guidelines
β
Additionally, OSHA has implemented stricter guidelines for the inspection and maintenance of construction equipment. Regular inspections of machinery and tools are now mandatory to ensure any potential safety hazard recognition and prevent accidents.Β
β
Employers must also provide proper training to employees and safety professionals for the safe operation of equipment to reduce the potential risks of injury.
β
Emphasis on Ergonomics
β
Another significant change is the emphasis on ergonomics in the workplace. OSHA now recommends the implementation of ergonomic solutions to prevent musculoskeletal disorders and other repetitive motion injuries among construction workers.Β
β
Employers are encouraged to provide ergonomic tools and mechanized equipment to create a more comfortable and safe working environment.
β
Overall, these recent changes and additions in OSHA compliance requirements for construction equipment demonstrate the agency's commitment to improving workplace safety and reducing the number of injuries in the construction industry.
Who Has to Comply With OSHA for Construction Fleet?
β
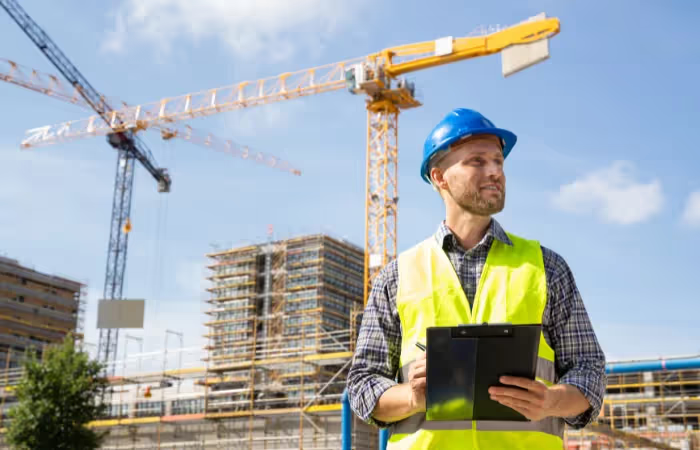
β
In the construction industry, all employers and employees must comply with OSHA regulations for construction equipment. This includes construction companies, contractors, subcontractors, and individual workers who are involved in any construction activities.Β
β
OSHA regulations are designed to ensure the safety and health of workers on construction sites by setting guidelines for the proper use of equipment, personal protective gear, and a construction safety checklist.
β
Employers are responsible for providing a secure work environment for their employees and ensuring that all types of equipment used on the job site meet OSHA standards. This includes conducting regular inspections of heavy construction equipment, providing proper training to employees on how to use the equipment safely, and implementing safety protocols to prevent accidents and injuries.
β
Workers also have a responsibility to comply with OSHA regulations for construction equipment. This includes following safety guidelines, using personal protective equipment as required, and reporting any potential hazards or unsafe conditions to their supervisors. By working together to comply with OSHA regulations, employers and employees can create a safer work environment and reduce the risk of accidents on construction sites.
β
Is OSHA Compliance for Construction Equipment Mandatory?
β
Yes, OSHA compliance for construction equipment is mandatory in order to keep the workers safe on job sites. OSHA has established specific standards to protect both experienced and entry-level workers from hazards associated with construction safety equipment. Employers are required to follow these regulations to maintain a safe working environment and prevent accidents and injuries.
β
Failure to comply with OSHA regulations for construction equipment can result in fines, penalties, and even shutdowns of job sites. The cost of non-compliance with OSHA regulations can vary depending on the severity of the violation. As per one study, In 2018, OSHA fines ranged from a maximum of $12,934 for minor infractions to $129,336 for willful or repeated violations.Β
β
Thus, it is essential for employers to prioritize effective safety and ensure that all equipment is in compliance with OSHA standards to protect the health and well-being of their workers.
β
Who is Exempted from OSHA Compliance Requirements?
β
While OSHA regulations apply to most businesses in the construction industry, there are certain exemptions for specific situations.Β
β
One exemption under OSHA heavy equipment regulations applies to small businesses with fewer than ten employees. These small businesses may be exempt from some OSHA requirements, including maintaining injury and illness-related detailed records, conducting specific types of training, and implementing certain safety programs.Β
β
However, it's important to note that even small businesses must still comply with OSHA's general duty clause, which requires providing a safe working environment free from recognized hazardous substances and hazardous materials.
β
Additionally, self-employed individuals who do not have any employees are also exempt from OSHA regulations. This exemption extends to independent contractors who work alone and do not employ any workers.
β
It's essential for businesses in the construction industry to understand their obligations under OSHA regulations and ensure they are in compliance with all relevant standards to maintain a safe and healthy work environment for their employees.
Download Our Equipment Maintenance Resources For Free!
Steps to Comply with OSHA Regulations
β
When it comes to ensuring a safe working environment on construction sites, compliance with OSHA regulations for construction equipment is crucial. With hazard assessment and by following these steps, your construction business can minimize the risk of accidents and injuries:
β
Regular Maintenance:Β
β
Regular maintenance of construction equipment is essential to ensure its safe operation. All equipment should be inspected for any signs of wear and tear, and any issues should be promptly addressed.
β
Proper Training:Β
β
All employees who operate construction equipment should receive proper training on how to use the equipment safely. This includes understanding the equipment's capabilities and limitations, as well as how to respond in case of an emergency.
β
Use Personal Protective Equipment (PPE):Β
β
Employees should always wear the appropriate PPE when operating construction equipment. This may include hard hats, gloves, safety goggles, respiratory protection, effective fire protection, and high-visibility clothing.
β
Follow Manufacturer Guidelines:Β
β
Construction management equipment should be used in accordance with the manufacturer's guidelines. This includes adhering to recommended operating & construction safety procedures and weight capacities.
β
Implement Fall Protection Measures:Β
β
For equipment that involves working at heights, such as cranes or scaffolds, fall protection measures should be in place. This may include guardrails, safety nets, or personal fall arrest systems.
β
Inspect Equipment Before Use:
Β
Before using any construction equipment, employees should inspect tools and equipment for any defects or malfunctions with the help of an equipment checklist. Any issues should be reported to a supervisor and the equipment should not be used until it is deemed safe.
β
By following these steps and staying up to date on OSHA regulations for construction equipment, construction companies can create a safer working environment for their employees and avoid costly fines for non-compliance.Β
β
ConclusionΒ
β
Creating a safe work environment for your construction fleet professionals starts with OSHA compliance. By following these regulations, you can significantly reduce the risk of accidents and injuries on your job sites.
β
However, achieving and maintaining OSHA compliance can be a complex task. This is where construction fleet management software like Simply Fleet can be a valuable asset.
β
Simply Fleet's fleet management software offers features like automated inspections and maintenance scheduling. With digital inspection checklists and safety data analysis, you can proactively manage fleets and ensure worker well-being.Β
β
By investing in a smart solution, you're not just helping yourself avoid non-compliance penalties but you're valuing your most important asset β your workforce.