Key Takeaways
Managing maintenance for a mixed fleet can be complex, but have you considered the benefits of a well-structured maintenance calendar? A Fleet Maintenance Calendar helps streamline the upkeep of trucks, service vehicles, construction equipment, and more, ensuring everything runs smoothly and safely. From daily inspections to annual overhauls, planning each maintenance task improves asset longevity, reduces downtime, and keeps your fleet road-ready.
This blog explores how to create a comprehensive maintenance calendar, streamline scheduling, and assign responsibilities to keep your fleet running efficiently year-round. Let’s explore the details and ensure your mixed fleet stays road-ready!
1. Comprehensive Fleet Inventory
Well-organized fleet information is the foundation for effective maintenance planning. By cataloging every asset in your fleet, you can gain valuable insights into your fleet composition, identify maintenance needs, and track asset performance.
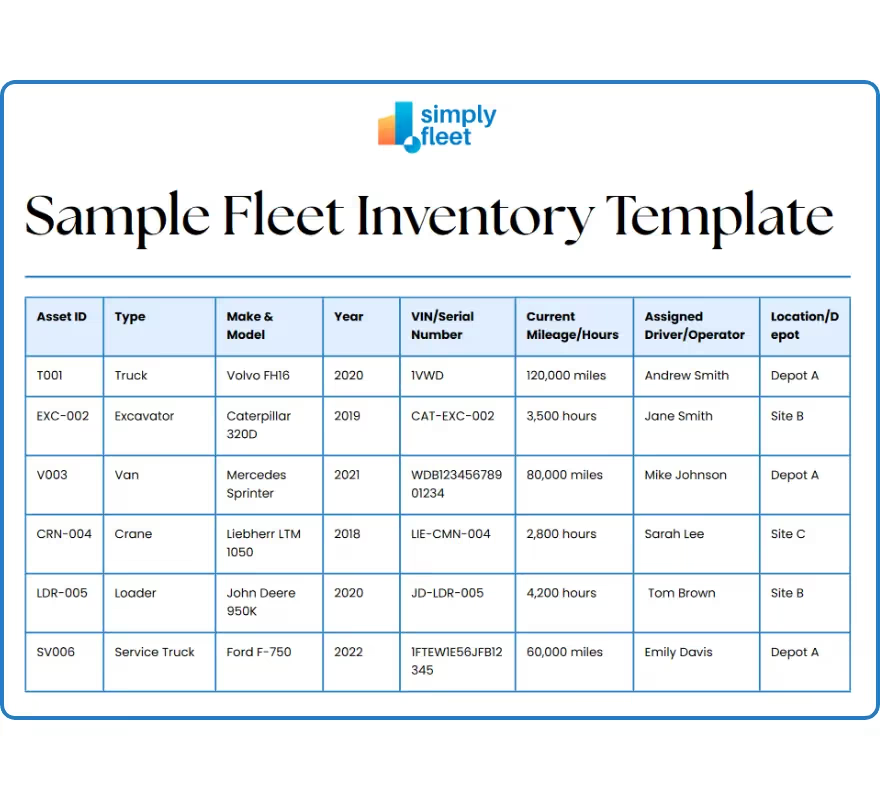
2. Define Maintenance Categories
Different types of assets within a fleet have varying maintenance needs. To effectively manage these needs, it's essential to categorize maintenance tasks based on frequency, type, and asset usage. Here’s a brief overview of maintenance categories based on frequency of operations:
Daily/Pre-Operation Checks are quick inspections performed by drivers or operators before using an asset. These checks ensure the asset is safe and operational for immediate use.
Weekly Inspections involve more detailed checks conducted by maintenance personnel. This level of inspection helps identify potential issues that may be absent during daily checks.
Monthly Maintenance includes routine tasks based on time or asset usage. These tasks might involve changing fluids, inspecting components, or addressing minor wear and tear.
Quarterly Maintenance focuses on preventative measures to address potential wear and tear and ensure the asset's reliability. This category often involves more in-depth inspections and component replacements.
Semi-Annual Maintenance is a comprehensive check that includes thorough inspections and part replacements. This maintenance level helps maintain the asset's health and prevent major breakdowns.
Annual Overhaul is an extensive service that covers all major systems of the asset. This is typically a time-consuming process that involves disassembling and inspecting components, replacing worn parts, and ensuring the asset is in optimal condition.
Usage-based maintenance is triggered by specific mileage, hours of operation, or other usage metrics. This approach allows for more tailored preventive maintenance schedules based on the actual usage of the asset.
Seasonal Maintenance is necessary to adjust the asset's performance and maintenance based on seasonal changes. This might involve preparing for winter conditions or adjusting to summer temperatures.
By categorizing maintenance tasks in this way, you can create a more efficient and effective maintenance schedule that addresses the unique needs of each asset in your fleet.
3. Detailed Maintenance Task Breakdown
Properly maintaining your fleet ensures its reliability, safety, and longevity. This section provides a detailed breakdown of maintenance tasks specifically tailored for trucks, service vehicles, construction equipment, and vans.
A. Trucks and Service Vehicles
The tasks specifically tailored for trucks and service vehicles are categorized based on the frequency and the scope of work, ensuring that your fleet remains in optimal condition.
Daily/Pre-Operation Checks are essential for daily vehicle safety. Drivers should inspect tire pressure, fluid levels, lights, and other critical components before each use. This proactive approach helps identify and address potential issues early on.
Weekly Inspections offer a more in-depth look at vehicle health. Maintenance teams should inspect battery condition, belts, hoses, brakes, and air filters, as well as lubricate key components. This ensures that potential problems are caught before they escalate.
Monthly Maintenance focuses on routine tasks that are crucial for maintaining vehicle performance. These tasks include regular oil changes, fluid level checks, tire rotations, and exhaust inspections.
Quarterly Maintenance is designed to prevent major issues from developing. It involves detailed brake system inspections, wheel alignments, suspension checks, cabin air filter replacements, and DEF flushes.
Semi-annual maintenance offers a more comprehensive check-up, including full fluid flushes, inspections of drive shafts and U-joints, DPF cleaning, and turbocharger testing.
Annual Overhaul is the most extensive maintenance task, involving major engine and transmission work, brake system overhauls, exhaust system replacement, and emission testing. This ensures that your vehicles are in top condition and comply with all regulations.
With this detailed breakdown, you can effectively manage the maintenance of your trucks and service vehicles, minimizing downtime and maximizing their lifespan.
B. Construction Equipment (Excavators, Cranes, Loaders, etc.)
This section outlines the specific maintenance tasks required for construction equipment, such as excavators, cranes, and loaders. These tasks are also categorized based on frequency and the scope of work involved.
Daily/Pre-Operation Checks are conducted by operators before each use to ensure the equipment is safe and operational. These checks include basic inspections for damage, fluid levels, tire/track conditions, attachments, and control systems.
Weekly Inspections are performed by maintenance teams to address more in-depth issues. This includes inspecting hydraulic components, lubricating grease points, cleaning air filters, checking battery health, and inspecting the cooling system.
Monthly Maintenance is focused on routine tasks such as oil changes, fluid level checks, brake inspections, fuel system inspections, and exhaust inspections. The frequency of these tasks is often based on the equipment's hours of operation.
Quarterly Maintenance involves more comprehensive checks, such as flushing and replacing hydraulic fluids, rotating or replacing tires/tracks, inspecting and lubricating attachments, replacing cabin air filters, and flushing coolant.
Semi-annual maintenance is a more extensive check that includes full fluid flushes, inspections of engine components, transmission checks, electrical system inspections, and steering and suspension system inspections.
Annual Overhaul is the most comprehensive maintenance task, involving major engine and hydraulic system overhauls, brake system overhauls, structural inspections, and emission testing.
Ensure your construction equipment is maintained in optimal condition by following this breakdown, minimizing downtime, and maximizing its lifespan.
C. Vans and Light Service Vehicles
Daily/Pre-Operation Checks for vans and light service vehicles are similar to those for trucks, focusing on basic safety inspections. Drivers should check tire pressure, fluid levels, lights, and leaks, and ensure cargo is secured properly.
Weekly Inspections by maintenance teams involve checking the health of the battery, inspecting belts and hoses, assessing the brake system, and verifying the condition of the air filter and HVAC system.
Monthly to Annual Maintenance for vans and light service vehicles follows a similar schedule to trucks, with adjustments made based on the specific vehicle's usage. This may include varying the frequency of oil changes, tire rotations, and other maintenance tasks.
By adhering to these maintenance guidelines, you can ensure the reliability and longevity of your vans and light service vehicles, contributing to the overall efficiency of your mixed fleet.
4. Seasonal Maintenance Tasks
This section outlines the specific seasonal calendar tasks that should be adjusted based on seasonal changes to ensure fleet readiness and longevity.
Winter Preparation
It is essential to ensure that your fleet can operate safely and efficiently in cold weather conditions. For trucks and service vehicles, this includes checking and topping off antifreeze levels, inspecting and replacing winter tires, testing heating and defrosting systems, and adding fuel additives to prevent diesel gelling.
For construction equipment, this process involves switching to winter-grade fluids, inspecting heating systems, checking for water contamination in fuel systems, and inspecting and replacing snow attachments.
Summer Preparation
This is equally important to ensure that your fleet can operate effectively in hot weather conditions. For trucks and service vehicles, this includes inspecting and testing air conditioning systems, checking coolant levels and hoses for leaks, and inspecting tires for heat-related damage.
For construction equipment, this process involves inspecting cooling systems for heat-related issues, lubricating moving parts to prevent rust, and ensuring air conditioning systems are operational.
By following these seasonal maintenance guidelines, you can help prevent breakdowns, reduce downtime, and ensure that your fleet is always ready to operate in any weather conditions.
5. Assign Responsibilities
Assigning clear responsibilities is essential for ensuring accountability and efficient maintenance operations within your fleet. With this approach, you can streamline processes, improve communication, and ensure that maintenance tasks are completed effectively.
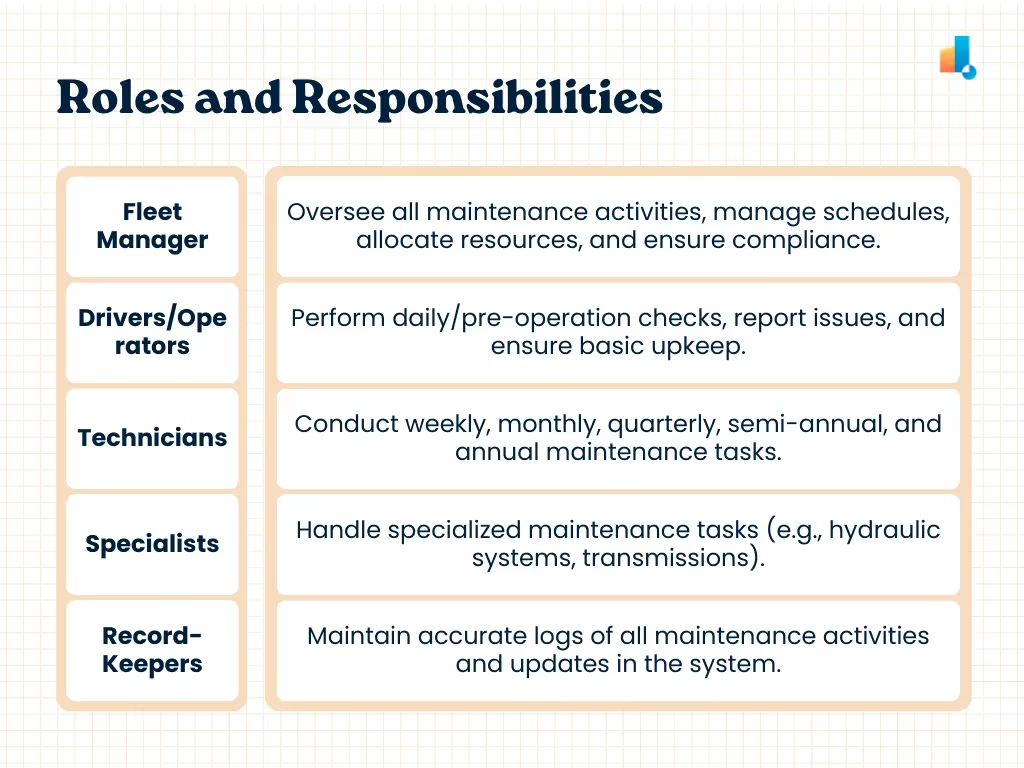
6. Utilize Fleet Maintenance Software
Fleet maintenance management software can significantly streamline the management of a mixed fleet. By automating scheduling, tracking maintenance activities, and generating detailed reports, this software can save time and resources.
Key features of such software include:
- Automated Scheduling: This feature allows you to set maintenance tasks based on specific time intervals, mileage, or hours of operation, ensuring that all assets receive timely maintenance.
- Alerts & Notifications: The software can send reminders for upcoming or overdue maintenance, preventing missed tasks and potential breakdowns.
- Maintenance Logs: Detailed records of all maintenance activities, parts used, and costs can be easily tracked and stored within the software.
- Reporting & Analytics: The software can generate reports on various KPIs such as downtime, repair costs, and equipment utilization, helping you identify areas for improvement.
- Mobile Access: Drivers and technicians can access and update maintenance information on their mobile devices, improving efficiency and reducing paperwork.
Some popular fleet maintenance software options include Simply Fleet, Fleetio, Samsara, MaintainX, and UpKeep. These software solutions offer a range of features to help you manage your fleet's maintenance effectively.
7. Record-Keeping and Tracking
Accurate record-keeping is crucial for effective fleet management. It ensures compliance with regulations, provides valuable data for audits, and helps optimize maintenance planning. Essential records include maintenance logs detailing tasks, dates, and personnel, service history for each asset, inspection reports, and compliance documentation.
By tracking key performance indicators (KPIs), you can gain valuable insights into your fleet's performance. Average maintenance cost per asset helps identify areas where costs can be reduced, while total downtime per asset highlights the reliability of your vehicles. Breakdown frequency indicates the overall health of your fleet, while fuel efficiency and asset utilization rates measure the efficiency of your operations.
With the upkeep of accurate records and tracking KPIs, you can make data-driven decisions to improve fleet performance, reduce costs, and ensure compliance with regulations.
8. Sample Preventive Maintenance Calendar For Mixed Fleet
This sample calendar provides a framework for integrating various asset types and scheduling maintenance tasks. You can customize this calendar to fit your specific fleet and operational needs.
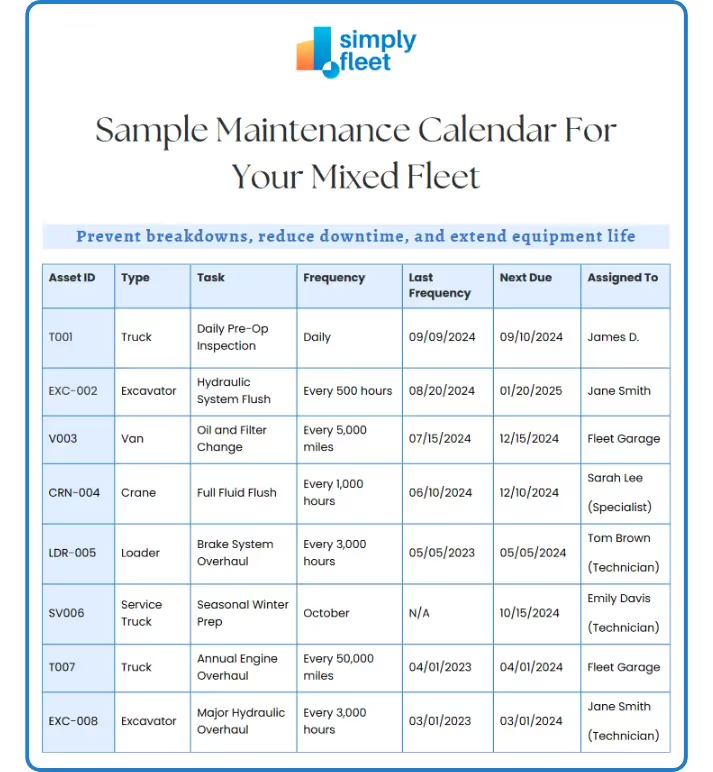
Download Our Free Maintenance Resources
- Fleet Vehicle Maintenance Log
- Vehicle Maintenance Checklist
- Pre-Trip Daily Vehicle Inspection Checklist
- Monthly Vehicle Inspection Checklist
- Annual Vehicle Inspection Checklist
- School Bus Pre-Trip Inspection Checklist
- Work Order Template
- Semi Truck & Trailer Pre-Trip Inspection Report
- Tow Truck Pre-Trip Inspection Checklist
- Free Excavator Safety & Daily Checklist Download (Excel)
- Crane Daily Inspection Form & Checklist Download
- Concrete Mixer Truck Inspection Checklist
- Daily & Monthly Crawler Inspection Checklists
- Free Daily Asphalt Paver Inspection Checklist & Report
9. Proactive Monitoring and Telemetry
Leveraging technology to monitor fleet health in real time is crucial for proactive maintenance and reducing unexpected downtime. Telematics and monitoring tools provide valuable insights into the performance and condition of your fleet.
GPS Tracking allows you to monitor the location, usage patterns, and operational hours of each asset. This information can help identify areas of high usage and potential maintenance needs.
Engine Diagnostics provides real-time data on engine performance, temperature, and potential faults. By monitoring these metrics, you can detect issues early and prevent them from escalating into more serious problems.
Fluid Level Sensors automatically monitor the levels of oil, coolant, and hydraulic fluid. This helps ensure that these critical fluids are always at the correct levels, preventing damage to equipment.
Vibration Sensors can detect unusual vibrations that may indicate mechanical problems. By identifying these issues early, you can schedule preventative maintenance and avoid costly repairs.
Remote Alerts provide instant notifications for critical issues such as overheating or low fluid levels. This allows you to take immediate action to address the problem and prevent further damage.
The benefits of using telematics and monitoring tools include:
- Early Problem Detection: By monitoring fleet health in real-time, you can identify and address issues before they escalate into major problems.
- Optimized Maintenance Scheduling: Based on actual usage and condition data, you can schedule maintenance tasks more efficiently, reducing downtime and costs.
- Enhanced Safety: By monitoring critical systems, you can prevent accidents caused by equipment failure.
10. Operator Training and Best Practices
To ensure the optimal performance and safety of your fleet, it is crucial to invest in comprehensive training for all personnel involved in fleet operations and maintenance.
Training Programs should cover a variety of topics, including:
- Daily Inspection Training: Equip drivers and operators with the skills to conduct effective pre-operation checks, identifying potential issues before they escalate.
- Maintenance Procedures: Provide technicians with in-depth training on proper maintenance techniques and safety protocols, ensuring that tasks are performed correctly and efficiently.
- Emergency Response: Prepare staff to handle breakdowns and emergencies effectively, minimizing downtime and preventing accidents.
- Software Utilization: Educate users on how to utilize fleet maintenance software effectively, maximizing its benefits and streamlining operations.
Best Practices for fleet management include:
- Consistent Documentation: Ensure that all inspections and maintenance tasks are accurately recorded, providing a valuable historical reference and supporting compliance efforts.
- Regular Audits: Conduct regular reviews of maintenance records and procedures to identify areas for improvement and ensure compliance with industry standards.
- Feedback Mechanism: Encourage operators and technicians to provide feedback on maintenance processes, fostering a culture of continuous improvement and innovation.
- Continuous Improvement: Stay updated with the latest maintenance technologies and methodologies to enhance fleet management practices and optimize efficiency.
By investing in training and adhering to best practices, you can create a highly effective and well-managed fleet that delivers optimal performance and minimizes downtime.
Related Posts
- How Preventive Fleet Maintenance Can Save Your Company Thousands
- Tips and Tricks to Create an Effective Fleet Maintenance Program
- Implementing Fleet Maintenance and Repair with Software
Conclusion
A Fleet Maintenance Calendar for a Mixed Fleet requires meticulous planning and organization to cater to the diverse needs of various asset types. By following the structured approach outlined above—comprehensive inventory, categorized maintenance tasks, clear responsibilities, effective use of technology, and ongoing training—you can ensure your fleet remains reliable, safe, and cost-effective.
Regularly review and adjust your maintenance calendar to adapt to changes in fleet composition, usage patterns, and technological advancements to maintain optimal fleet performance.